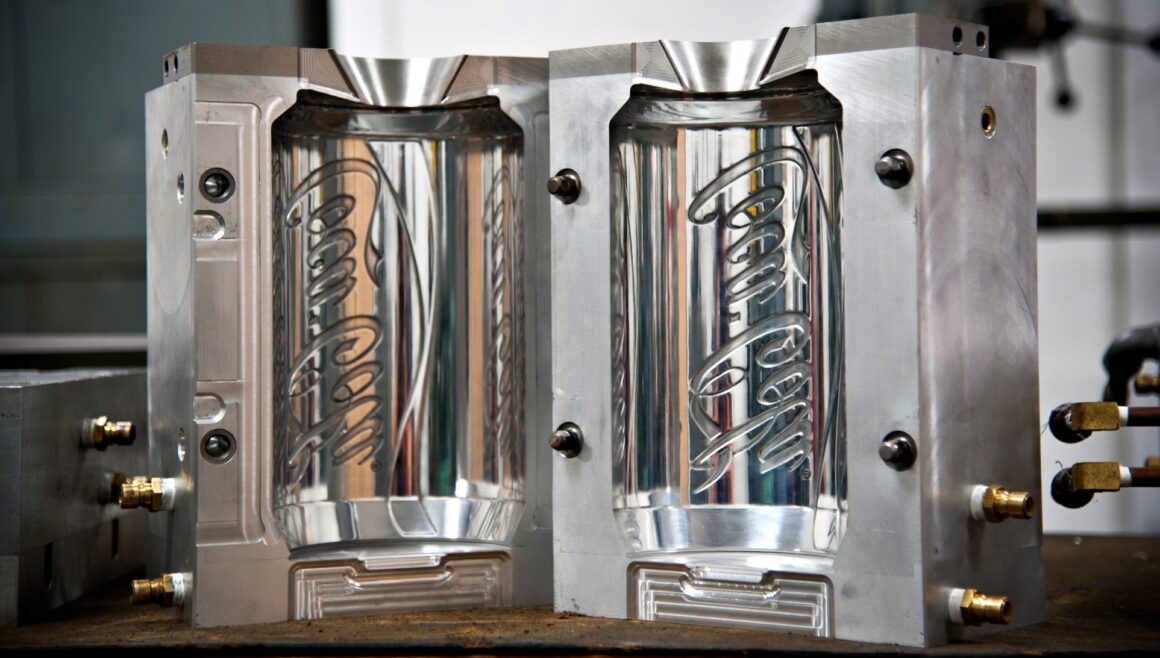
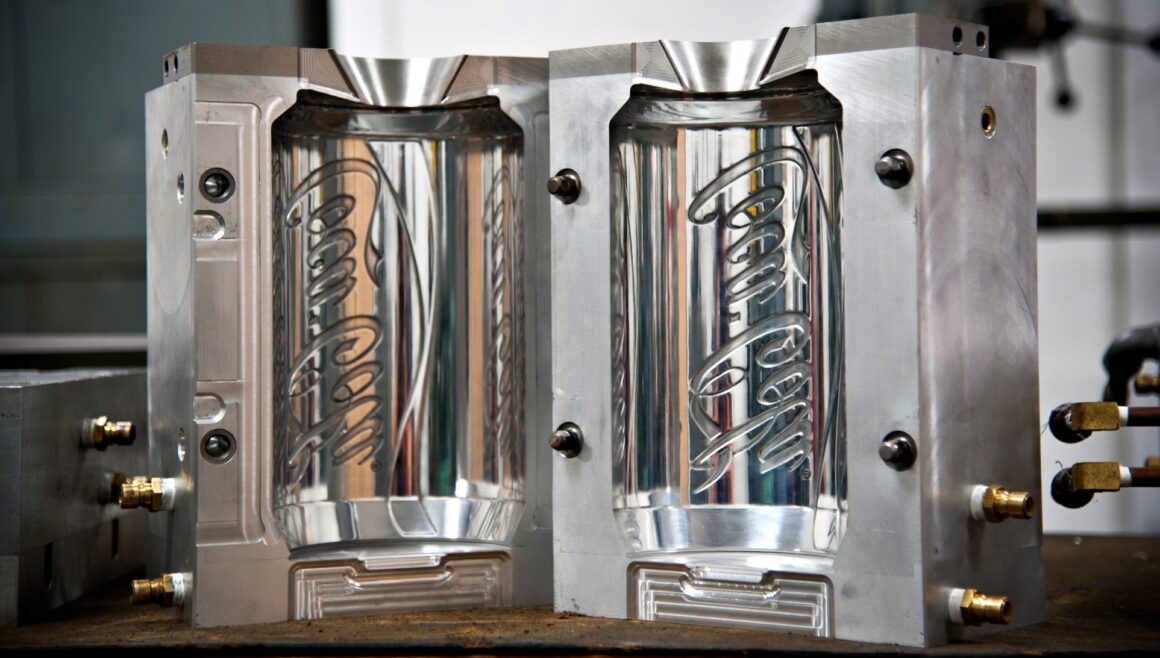
Mold manufacturing is the process of creating molds or tooling that are used to produce various products through techniques such as injection molding. These molds are typically made from materials such as steel or aluminum and are designed to shape and form raw materials into specific shapes and sizes. Mold manufacturing plays a crucial role in various industries, including automotive, aerospace, consumer goods, and medical devices.
In the automotive industry, mold manufacturing is essential for producing components such as dashboards, bumpers, and interior trims. These molds allow for the mass production of these parts with high precision and consistency. In the aerospace industry, mold manufacturing is used to create complex components such as turbine blades and aircraft interiors. The ability to produce these parts with tight tolerances is critical for ensuring the safety and performance of aircraft.
The consumer goods industry also heavily relies on mold manufacturing for the production of items such as plastic bottles, toys, and electronic devices. Injection molding, which is the most popular method of mold manufacturing, allows for the efficient production of these items in large quantities. In the medical device industry, mold manufacturing is used to produce components such as syringes, catheters, and implants. The ability to manufacture these parts with high precision and cleanliness is crucial for ensuring patient safety.
The Most Popular Mold Manufacturing Method: Understanding Injection Molding
Injection molding is the most popular method of mold manufacturing due to its versatility and efficiency. It involves injecting molten material into a mold cavity under high pressure, which then solidifies and takes the shape of the mold. This process allows for the production of complex parts with high precision and consistency.
One of the main advantages of injection molding over other methods is its ability to produce parts with intricate details and complex geometries. The high pressure used in injection molding allows for the material to flow into even the smallest crevices of the mold, resulting in highly detailed parts. This makes injection molding ideal for producing items such as gears, connectors, and electronic components.
Another advantage of injection molding is its ability to produce parts in large quantities. Once the mold is created, the injection molding process can be automated, allowing for the production of thousands or even millions of parts with minimal human intervention. This makes injection molding a cost-effective solution for mass production.
In comparison to other mold manufacturing methods such as blow molding or rotational molding, injection molding offers greater design flexibility and faster production cycles. It also allows for the use of a wide range of materials, including thermoplastics, thermosetting plastics, and elastomers.
The History and Evolution of Injection Molding Technology
The history of injection molding dates back to the late 19th century when John Wesley Hyatt invented the first injection molding machine. This machine used a plunger to inject celluloid into a mold cavity, allowing for the production of billiard balls. However, it wasn’t until the 1940s that injection molding gained widespread popularity with the development of new materials and improved machinery.
One of the major milestones in the evolution of injection molding technology was the introduction of screw injection machines in the 1950s. These machines allowed for more precise control over the injection process and enabled the use of a wider range of materials. The 1970s saw further advancements in injection molding technology with the introduction of computer numerical control (CNC) machines, which allowed for greater automation and improved accuracy.
Today, injection molding technology has reached new heights with the integration of robotics, computer-aided design (CAD), and computer-aided manufacturing (CAM) systems. These advancements have made it possible to produce highly complex parts with tight tolerances and reduced cycle times. Additionally, new materials such as biodegradable plastics and composites have expanded the capabilities of injection molding even further.
The Science Behind Injection Molding: How It Works
The injection molding process consists of four stages: clamping, injection, cooling, and ejection. Each stage plays a crucial role in the overall process and requires careful control and monitoring.
The clamping stage involves closing the mold and holding it securely in place. This is done using hydraulic or mechanical clamps that exert pressure on the mold halves. The clamping force must be sufficient to withstand the high pressure of the injection stage and ensure that the mold remains closed during the entire process.
In the injection stage, the molten material is injected into the mold cavity under high pressure. This is done using an injection unit that consists of a hopper, a screw or plunger, and a nozzle. The material is fed into the hopper, where it is heated and melted. The screw or plunger then pushes the molten material through the nozzle and into the mold cavity.
Once the material has been injected into the mold cavity, it begins to cool and solidify. The cooling stage is critical for ensuring that the part retains its shape and dimensions. Cooling can be achieved through various methods, such as circulating water or air around the mold. The cooling time depends on factors such as the material being used and the complexity of the part.
After the part has cooled and solidified, it is ready to be ejected from the mold. The ejection stage involves separating the mold halves and removing the part from the mold cavity. This is done using ejector pins or plates that push against the part and force it out of the mold. Care must be taken to ensure that the part is ejected without any damage or deformation.
Materials Used in Injection Molding and Their Properties
Injection molding can be used with a wide range of materials, each with its own unique properties and characteristics. The choice of material depends on factors such as the desired properties of the final part, the intended application, and cost considerations.
Thermoplastics are the most commonly used materials in injection molding. These materials can be melted and solidified multiple times without undergoing any significant changes in their properties. They offer a good balance of strength, flexibility, and chemical resistance. Some common thermoplastics used in injection molding include polypropylene, polyethylene, polystyrene, and ABS.
Thermosetting plastics are another type of material used in injection molding. Unlike thermoplastics, these materials undergo a chemical reaction during the curing process, which makes them hard and rigid. Once cured, thermosetting plastics cannot be melted or reshaped. They offer excellent heat resistance and dimensional stability. Examples of thermosetting plastics include epoxy, phenolic, and melamine.
Elastomers, also known as rubber-like materials, are used in injection molding to produce flexible parts with high elasticity. These materials can be stretched and deformed without undergoing permanent deformation. Elastomers offer excellent resistance to impact, abrasion, and chemicals. Some common elastomers used in injection molding include silicone, polyurethane, and natural rubber.
The properties of the material used in injection molding can be further enhanced by adding fillers or reinforcements. Fillers such as glass fibers or mineral powders can improve the strength and stiffness of the part. Reinforcements such as carbon fibers or Kevlar can enhance the mechanical properties of the material, making it suitable for high-performance applications.
The Role of Design and Prototyping in Injection Molding
Design and prototyping play a crucial role in the success of an injection molding project. Proper design and prototyping ensure that the final part meets all the requirements in terms of functionality, aesthetics, and manufacturability.
During the design phase, engineers work closely with designers to develop a 3D model of the part using CAD software. This allows for a detailed analysis of the part’s geometry, dimensions, and features. Design considerations such as draft angles, wall thickness, and gate locations are taken into account to ensure that the part can be successfully manufactured using injection molding.
Prototyping is an essential step in the injection molding process as it allows for the testing and validation of the design before mass production. Prototypes can be created using various methods such as 3D printing, CNC machining, or silicone molding. These prototypes are then evaluated for fit, form, and function to identify any design flaws or improvements that need to be made.
Tools such as mold flow analysis software are used during the design and prototyping phase to simulate the injection molding process and predict potential issues such as warpage, sink marks, or air traps. This allows engineers to make necessary adjustments to the design before investing in expensive molds.
The Injection Molding Process: Step-by-Step Guide
The injection molding process consists of several stages that must be carefully executed to ensure the production of high-quality parts. Here is a step-by-step guide to the injection molding process:
1. Clamping: The mold halves are closed and held securely in place using hydraulic or mechanical clamps. The clamping force must be sufficient to withstand the high pressure of the injection stage.
2. Injection: The molten material is injected into the mold cavity under high pressure. This is done using an injection unit that consists of a hopper, a screw or plunger, and a nozzle. The material is fed into the hopper, where it is heated and melted. The screw or plunger then pushes the molten material through the nozzle and into the mold cavity.
3. Cooling: Once the material has been injected into the mold cavity, it begins to cool and solidify. The cooling stage is critical for ensuring that the part retains its shape and dimensions. Cooling can be achieved through various methods, such as circulating water or air around the mold. The cooling time depends on factors such as the material being used and the complexity of the part.
4. Ejection: After the part has cooled and solidified, it is ready to be ejected from the mold. The ejection stage involves separating the mold halves and removing the part from the mold cavity. This is done using ejector pins or plates that push against the part and force it out of the mold. Care must be taken to ensure that the part is ejected without any damage or deformation.
Quality Control in Injection Molding: Ensuring Consistency and Precision
Quality control is a critical aspect of injection molding as it ensures that each part meets the required specifications in terms of dimensions, appearance, and functionality. Quality control measures are implemented at various stages of the injection molding process to detect and correct any defects or deviations.
One of the key quality control methods used in injection molding is process monitoring. This involves continuously monitoring and recording various parameters such as temperature, pressure, and cycle time during the injection molding process. Any deviations from the set parameters can indicate potential issues with the process or the mold.
Another important quality control method is inspection and testing. This involves visually inspecting each part for any defects such as flash, sink marks, or warpage. Dimensional inspection is also performed using tools such as calipers, micrometers, or coordinate measuring machines (CMMs) to ensure that each part meets the required tolerances.
Statistical process control (SPC) is another quality control method used in injection molding. SPC involves collecting and analyzing data from multiple parts to identify any trends or patterns that may indicate a problem with the process. This allows for timely adjustments to be made to prevent further defects.
Tools such as mold flow analysis software are also used in quality control to simulate and optimize the injection molding process. These tools can predict potential issues such as warpage, sink marks, or air traps, allowing engineers to make necessary adjustments to the process or the mold design.
Advantages and Disadvantages of Injection Molding
Injection molding offers several advantages over other mold manufacturing methods, but it also has some limitations. Here are the main advantages and disadvantages of injection molding:
Advantages:
1. High precision and consistency: Injection molding allows for the production of parts with tight tolerances and high repeatability. This ensures that each part meets the required specifications.
2. Cost-effective for mass production: Once the mold is created, the injection molding process can be automated, allowing for the production of thousands or even millions of parts with minimal human intervention. This makes injection molding a cost-effective solution for mass production.
3. Design flexibility: Injection molding allows for the production of parts with complex geometries and intricate details. The high pressure used in injection molding allows for the material to flow into even the smallest crevices of the mold, resulting in highly detailed parts.
4. Wide range of materials: Injection molding can be used with a wide range of materials, including thermoplastics, thermosetting plastics, and elastomers. This allows for greater design flexibility and the ability to meet specific requirements such as strength, flexibility, or chemical resistance.
Disadvantages:
1. High initial investment: The cost of creating molds for injection molding can be high, especially for complex parts or small production runs. This can make it less suitable for prototyping or low-volume production.
2. Long lead times: The process of creating molds for injection molding can take several weeks or even months, depending on factors such as complexity and size. This can result in longer lead times compared to other manufacturing methods.
3. Limited part size: Injection molding is typically used for producing small to medium-sized parts. Large parts may require specialized equipment or multiple molds, which can increase costs and complexity.
4. Material limitations: While injection molding can be used with a wide range of materials, there are some limitations in terms of temperature resistance, chemical resistance, or mechanical properties. Some materials may also require special handling or processing conditions.
Applications of Injection Molding in Different Industries
Injection molding is widely used in various industries due to its versatility and efficiency. Here are some examples of industries that rely on injection molding for the production of their products:
1. Automotive: Injection molding is used in the automotive industry to produce components such as dashboards, bumpers, interior trims, and door panels. The ability to produce these parts with high precision and consistency is critical for ensuring the safety and performance of vehicles.
2. Aerospace: Injection molding is used in the aerospace industry to produce components such as turbine blades, aircraft interiors, and structural parts. The ability to manufacture these parts with tight tolerances and high strength-to-weight ratios is crucial for the performance and efficiency of aircraft.
3. Consumer goods: Injection molding is widely used in the consumer goods industry for the production of items such as plastic bottles, toys, electronic devices, and household appliances. The ability to produce these items in large quantities with high precision and consistency is essential for meeting consumer demand.
4. Medical devices: Injection molding is used in the medical device industry to produce components such as syringes, catheters, implants, and surgical instruments. The ability to manufacture these parts with high cleanliness and dimensional accuracy is critical for ensuring patient safety.
5. Packaging: Injection molding is a common method used for packaging products. It involves injecting molten material, such as plastic or metal, into a mold cavity. The material then cools and solidifies, taking the shape of the mold. Injection molding allows for the production of complex and precise packaging designs, making it ideal for creating containers, caps, and other packaging components. This process is efficient and cost-effective, as it can produce large quantities of packaging quickly. Additionally, injection molding offers excellent durability and strength, ensuring that the packaging can protect the product throughout its lifespan.
Read more similar articles HERE